Operational Support
Process Model Benchmarking, Plant Optimization, and Production Impact Analysis
To accurately capture the impacts of key process parameters on production during plant optimization, highly precise and faster process models are required. The inherent complexity of certain processes can hinder achieving accurate results timely through steady-state simulations. Dynamic models provide an effective solution by facilitating faster convergence of closed refrigerant loops and enabling key equipment parameters to be highly adaptive. Unlike the plant itself, an accurate dynamic model allows certain variables to be adjusted while keeping others fixed, thus capturing the true impact of the modified parameters.
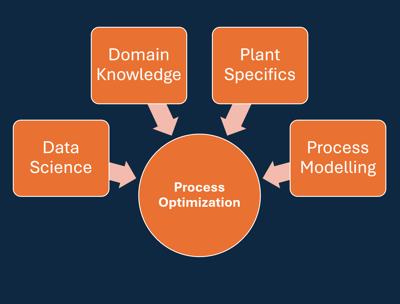
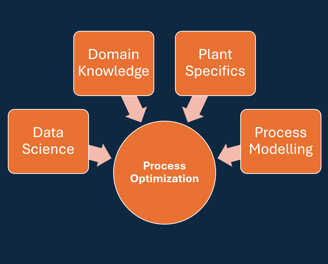
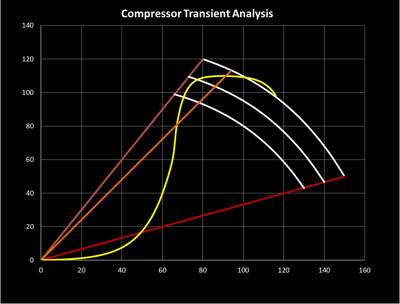
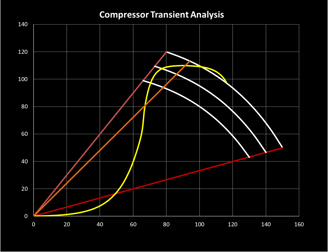
High Fidelity Customized Dynamic Simulations
For simulating complex processes such as compressor surge, expander operation, choked flow, tube rupture, and rapid transient scenarios, high-fidelity models can be developed to focus on specific parts of the plant in isolation. These models run with smaller time steps and incorporate more detailed information to accurately represent reality.
The integration of historical operational data, domain knowledge, process simulation, and plant-specifics creates a powerful combination that offers invaluable insights into operations. This synergy enables reliable predictions of production impacts, comprehension of sequential production limiters, identification of safe operating limits (SOL), and leading indicators of potential failures. These are just some of the many benefits that this comprehensive approach can provide.
Historical Plant Data Analysis Through Data Science Backed by Process Simulation
Through years of developing and utilizing process models for operational plants, we have endeavored to understand the capabilities and limitations of process simulators. We identify the necessary non-idealities that must be incorporated into the model to enhance its representation of reality. Additionally, we determine the adjustments required to ensure reliable predictions when the model is extended into uncharted territories.
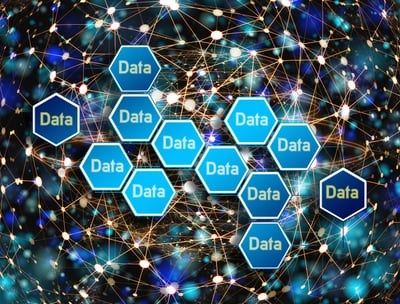
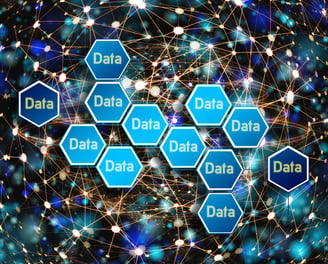
Control Loop Design, Start-up and Shutdown Procedure Development and Improvement
A dynamic model of the facility can be specifically built to accurately simulate the amplitude and timing of the responses following process changes. This model can then be utilized to design or test the control loop, ranging from simple feedback control to more complex feedforward, multi-input and output, or inferential control systems. Additionally, it can be applied to develop or test startup and shutdown procedures. Previous experiences have demonstrated that gas velocity can exceed limits within a compressor loop during startup, posing the risk of vibration and potential damage to certain components.
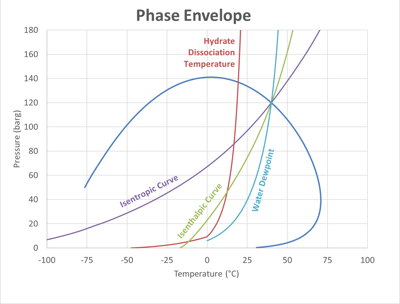
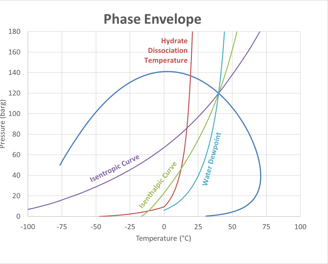
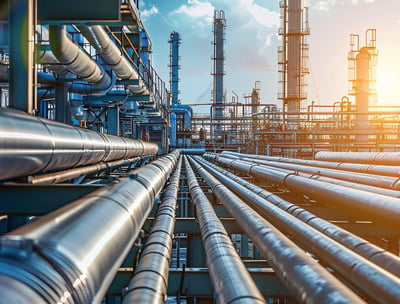
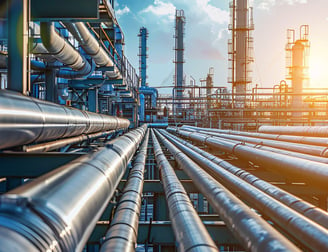
Reliable PVT Analysis Using Accurate Models for Challenging Components
The presence of components such as water, MEG, TEG, CO2, H2S, and Hg in the feed to an oil and gas processing or LNG plant presents challenges that necessitate accurate phase envelope and PVT prediction. Issues such as water dropping out from a CO2 stream after cooldown, heavy hydrocarbon freeze-out, hydrate formation, liquid mercury dropout, and free sour water formation can cause asset damage and pose risks to personnel and the environment. Understanding how these components partition in different phases is essential to mitigate these risks.
APC serves as the brain of your plant, capable of being trained to navigate the plant through a diverse range of operating scenarios. High-fidelity process models can be employed to conduct step tests and generate data within a safe environment. These representative process models can explore operational territories that may not be feasible or safe to attempt on the actual plant. Our team has extensive experience in building, training, and enhancing APC systems for LNG plants over several years of operation.
Advanced Process Control (APC) Development Support
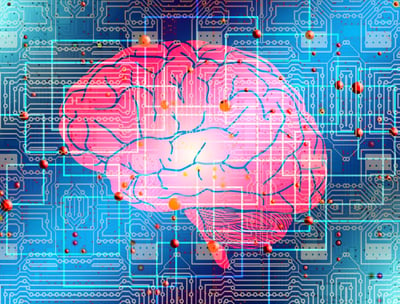
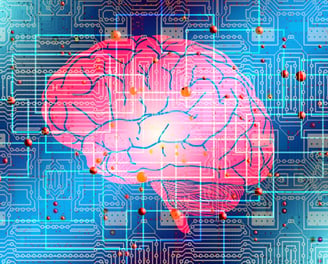
Comprehensive Dynamic Assessment of Equipment Capacities and Transient Operational Conditions
Key equipment in gas processing and LNG plants experience varied conditions during startups and shutdowns, markedly different from steady-state operations. Understanding the changes in actual capacities over time, along with excursions during different operational modes, and their impact on fatigue life is crucial. This knowledge enables proactive decision-making to minimize threats to integrity, deviations, and downtime.
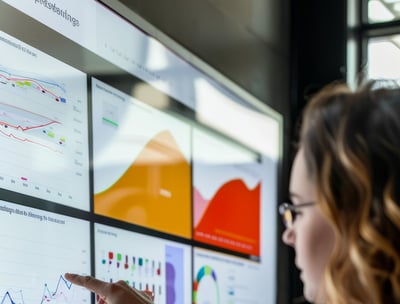

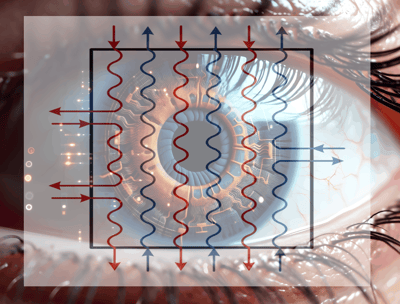
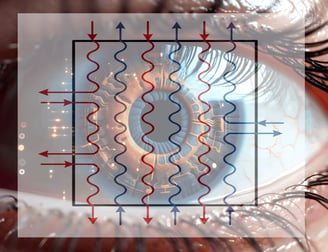
Dynamic Modeling of Component Accumulation and Equilibrium in Process Units
There are situations where various components cannot exit a unit due to operating conditions that prevent their partitioning in the unit’s outlet streams. These components accumulate in the system, reaching new equilibrium conditions that can differ significantly from steady-state results. Such scenarios can only be accurately modeled in dynamic mode. Examples include mercury, aromatics, and certain midrange hydrocarbons remaining in condensate stabilization units or compression units.
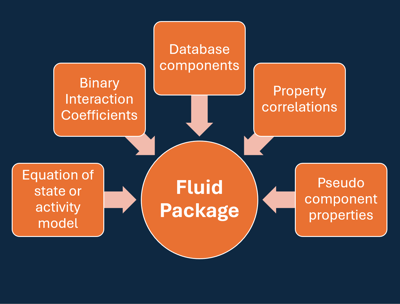
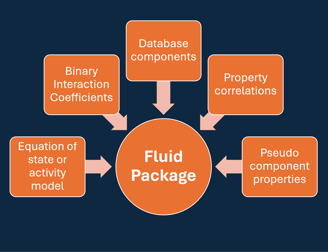
Fluid Characterization
Fluid packages are the fundamental building blocks of every process model. The accuracy of the entire model hinges on the fluid package being a true representation of the fluid being processed. All elements of the fluid package must be meticulously chosen and characterized to ensure that the PVT calculations accurately reflect real-world conditions.
When a plant processes multiple reservoir fluids, employing the Common Pseudo approach is crucial to minimize the number of components and enhance the convergence speed of the process model. At NEURHINE, we offer comprehensive fluid characterization and tuning for both single and multiple fluids, utilizing the latest techniques and tools.
Process Safety Design and Analysis
Dynamic analysis of PSV Relief Load and Blowdown System
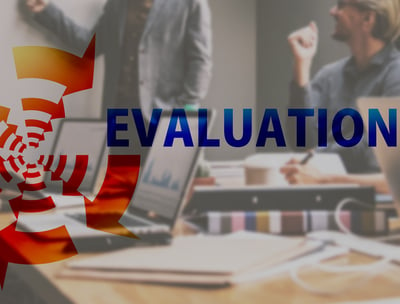
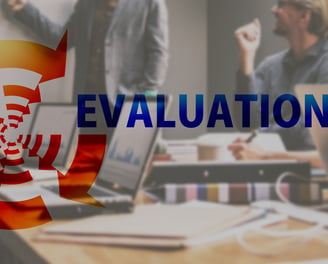
In our experience, there have been several instances where a Pressure Safety Valve (PSV) deemed inadequate based on simple steady-state simulations was proven to be adequate through dynamic analysis. Notably, PSVs at the discharge of compressors and the overhead of distillation columns have been reassessed in this manner. A rigorous dynamic model can incorporate process realities that are not considered in a steady-state model.
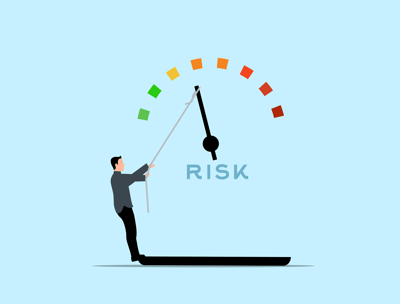
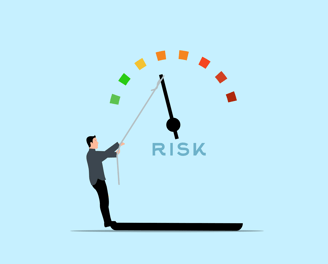
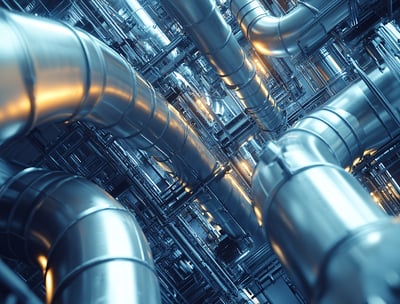
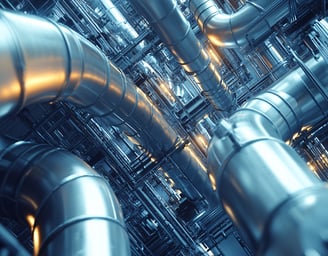
Dynamic Assessment of Safety Instrumented Functions (SIF) and Process Safety Time (PST)
High-fidelity dynamic models can be developed and used to assess the effectiveness of a Safety Instrumented Function (SIF) that serves as an Independent Protection Layer (IPL). Additionally, dynamic analysis is employed to calculate Process Safety Time (PST) in situations where the process dynamics make it challenging to rely on simple steady-state calculations for PST.
The required orifice area of a Pressure Safety Valve (PSV) might be significantly underestimated if the appropriate method is not employed during sizing. The presence of gas, whether as part of a two-phase or flashing liquid entering the PSV, or a scenario where liquid is pushed into the PSV by gas, can notably alter the required area. Utilizing a rigorous model allows for an accurate assessment of a PSV in such situations, incorporating geometry, static head, and the dynamic nature of the process into the calculations.
Rigorous Assessment of Load on PSVs in Two-Phase Flow, Flashing Liquid, or Liquid-Pushed-By-Gas Scenarios
Cutting pipes and installing new devices due to capacity shortages or mission time may not always be the optimal solution. By incorporating high-fidelity dynamic assessments that account for the realities of the process, downtime and the costs associated with physical modifications can be significantly reduced.
Process Design Support
Steady State Modelling and Simulation
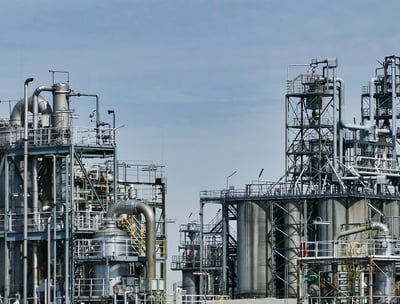
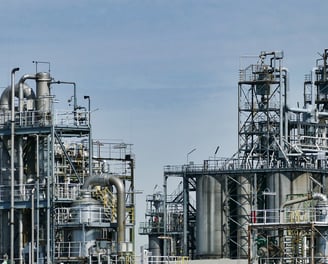
Steady-state process models are employed across a broad spectrum of applications. These range from testing conceptual designs to simulating plant operations and generating Heat and Material Balance data essential for equipment sizing and hydraulic calculations.
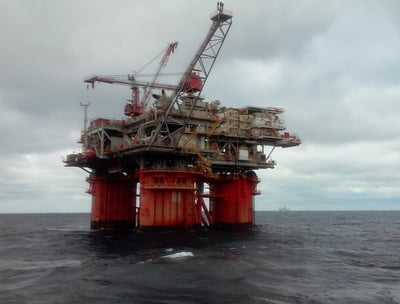
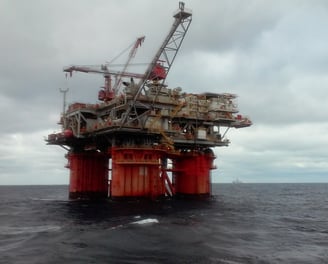
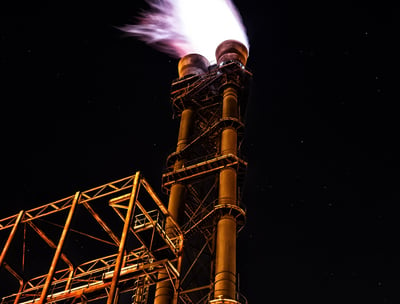
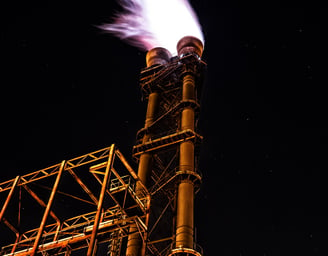
Dynamic Process Simulation for Design Phase
Steady-state models may not capture all aspects of a process when complexity exceeds a certain level. We develop dynamic process models that incorporate real-world conditions and non-idealities observed from past experiences. The rapid convergence, adaptability, and accuracy of these dynamic models allow for the simulation of multiple operating scenarios, ensuring that the governing case is used for equipment sizing. Our tools for interacting with simulator packages significantly enhance efficiency, enabling us to model several cases and determine the optimal design case.
The transient nature of a flare system necessitates a dynamic assessment for more representative simulation. Steady-state analysis overlooks the significant volume and metal mass of the headers. Consequently, a dynamic assessment that incorporates these factors yields less conservative back pressure estimates and higher Minimum Design Metal Temperature (MDMT).
Dynamic Analysis of Flare System
Leveraging years of experience in troubleshooting, debottlenecking, root cause analysis, and plant operations, applied to both greenfield designs and brownfield modifications.
Developing Reliable and Accurate Process Models for CO2 Sequestration
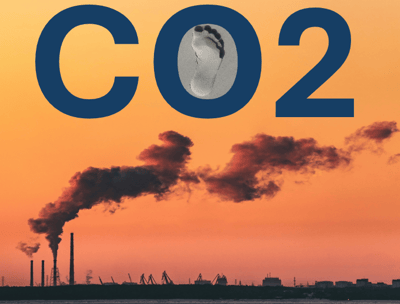
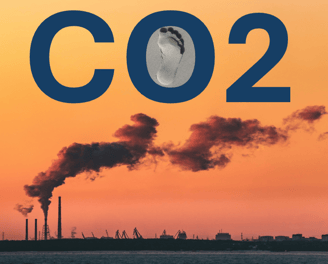
Creating a reliable process model for a CO2 compression unit presents significant challenges without real-life operational data. Through our previous experience of benchmarking a running unit, we have identified several key challenges:
Enthalpy calculation difficulties when crossing the critical point, which can impact compressor power.
Sudden phase changes or flips between dense phase, liquid, and gas.
Accurate prediction of water content and dew point in the gas, liquid, and dense phase CO2.
Hydrocarbon and BTEX accumulation in the unit.
Issues related to cooldown and water dropout.
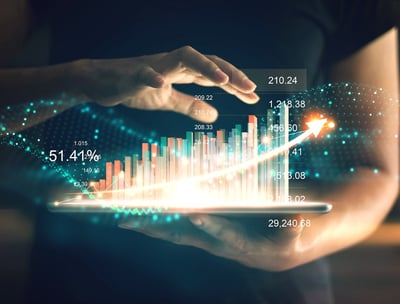
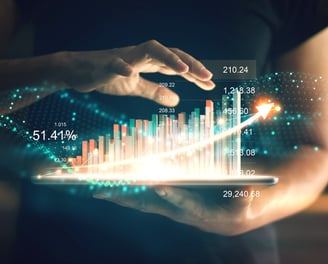
Debottlenecking During Design Phase: Unlocking Efficiency and Reliability
By creating a high-fidelity, representative process model, incorporating parameters that define equipment performance, efficiency, and hydraulics, adaptive to varying throughput and operating conditions.
Leveraging past operational experiences from similar facilities and advanced data science techniques to improve reliability of predictions from the model.
Then utilize the model to simulate multiple “Check Cases” for different operational modes, feed compositions, and conditions—both steady-state and transient.
This approach allows to identify and proactively resolve potential bottlenecks and operational issues.
Addressing these issues early can prevent loss of production opportunities (LPO) or the need for the plant to operate at suboptimal conditions waiting for the next turnaround.
© 2025. All rights reserved.
NEURHINE Process Solutions